ローレット付き特殊ビス
ご要望
「材料費が高騰してしまい、既存の取引メーカーの製造コストが上昇して困っている。何とか解決できないだろうか?」
POINT
- 長年培った知識、技術、ノウハウを持つスタッフによる徹底的なヒアリング
- 余分な工程の洗い出し
- 製造・加工設備をもつ充実した工場による作業工程の自動化により、工程削減
完成までを振り返って
パソコンに使用される小さな特殊ビス。
市場的な需要が高い時期で、生産量とコストダウンにチャレンジした製品でした。
当時を振り返って、担当者の対談模様をお届けいたします。
―月7万個の生産、コストダウンへのチャレンジ
「このねじの提案時って、ちょうどXPへの切り替えのピーク時やったなぁ。」
「1日2,000~3,000個、月に7万個製造しないと間に合わへん状況で、量産といかにコストダウンするかが課題でした。」
「たしか、はじめは転造加工の依頼やったけど、トータルで生産してコストダウンできるんちゃうかっていう話になって。
それで後藤部長が“チャレンジする価値はある!”と判断して、お客様に”ぜひやらせてください!”と提案したんでしたよね?」
「やっぱり、お客様の話をしっかり聞いてみんとあかんよね。じゃないと、ベストな提案はできひん。」
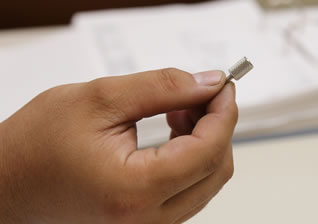
―難航した金型製造と量産
「まず金型作りから始めようということで、材料屋や金型屋に相談しにいったら、”金型を製造する際の絞り加工が、これでは計算上実現不可能や”って言われて。」
「そうそう(笑)。でも”やってみな分からん”ってことで、何回も試作しました。
ポイントは、線材、表面処理、金型、超特殊潤滑油。この4つ。この組み合わせでした。」
「何回試作したやろ。細かい修正と、各工程をちょっとずつ変えて。
最初はバラつきがあったけど、最後の最後でピッタリの金型が完成して、あの瞬間は、製造業者やったらみんなそうやと思うけど、嬉しかったわ。」
「金型が完成して可能性が開けましたよね。これで量産が可能になりましたし
ただ、その後も切削加工漏れとか、いろんなアクシデントがありましたけど。」
―コスト、納期面でも満足してもらえる結果に
「お客様に納品したとき、コストダウンはもちろんやけど、金型ができたことで量産が可能になって、結果的に納期の早さにもかなり驚いてもらえたのはよかったですね。」
「冷間加工やったら、1日に4~5万本製造できますもんね。」
「かなり難しかったけど、鉄の品質も日進月歩、良くなっているんやなと実感した。
それが故に公式を打ち破る結果につながった。ねじってやっぱり無限大やで。
しんどいけど、挑戦したらそのぶん新しい発見があって、やっぱり、ねじ造りはオモロイよな。」
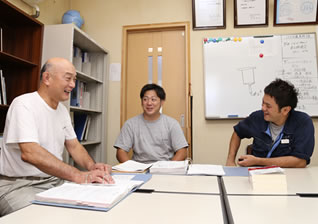