「安かろう悪かろう」の海外生産のねじを国内生産に切り替えて課題を解決!
ご要望
「海外で生産しているローレット付きの特殊なビスに問題がある。加工工程に抜け漏れがあり品質が悪く、さらに出荷前の選別に問題があり不良品が多い。この2点を解決したい。なんとかならないだろうか。」というご要望をいただきました。
POINT
- 工程ごとの加工方法の確認と検討
- 最適な方法による加工の実施
- 特殊な潤滑油の発見と利用
- 自動選別機による選別で粗悪な製品激減
完成に至るまでのストーリー
弊社の製造管理者の後藤が完成までのストーリーを振り返りました。
新人研修の一環で語っていた内容を抜粋いたします。
お客様からの具体的なご要望を教えてください!
「その前にねじの概要について説明しよう。ローレット付きの特殊なビスなんだけど、これは複雑な加工が複数必要。簡単にできる代物じゃないし、加工工程や選別に問題があると不良率も高くなる。当初お客様が依頼していたねじ屋さんはこれを海外で生産していたみたい。残念なことに問題も多く、加工漏れと最終的な選別が相まって不良率がめちゃくちゃ高かったとのこと。それをなんとかしてほしい!っていう依頼やってん。」
「よくわかりました。まずは問題点を詳しくヒアリングしたと思うのですが、その内容について教えてください。」
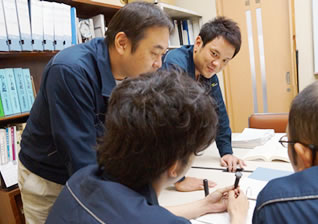
「問題点を明確にするためには、どのような工程で作られているのかを確認すること。お客様に確認すると大きく分けて6工程に分かれていた。1. ヘッダー加工、2. 切削加工( 1 )、3. 切削加工( 2 )、4. 転造加工( 1 )、5. 転造加工( 2 )、6. 選別、という工程。問題点は2点あり、「2. 切削加工( 1 )」が抜けてしまいで次に控えている切削加工でトラブルが発生すること。そして最後の選別の質が低く不良品が出荷品に混じること。この2点が問題であることがわかった。」
「問題点を整理する前にどのような工程で製造されているのかを確認することで、お客様とも話がしやすくなりそうですし、イメージしやすくなりますね!」
「その通り!「2. 切削加工( 1 )」ではM3の転造下径まで削っていたようだけど、最初のヘッダー加工時点でできないかな?と頭の中で考えた。でもその時点では本当に出来るかわからない。わからなければ作って試してみよう!と思って挑戦することにした。」
「工程を整理することで解決するための工夫を凝らすポイントの仮説が立てやすい、だから挑戦できる、ということでしょうか。」
「頭の中で『うちで作るなら…』を考えることで仮説が立てやすくなる。ヘッダーブランクである程度作りこみをするにしても金型代だけで数十万円もかかってしまう。だからこそ金型メーカーと検討を重ねた。ここからが試行錯誤の連続。絞りをヘッダーで出来るかを確認したけど、金型メーカーの担当者様から『過去にこんなことを成功したことも、しようとしたこともない。できるかな。う~ん。』というお返事。」
「どうやって説得したんですか?」
「『失敗しても責任などは負わなくても良い!だからどうか作ってほしい!』と心からお願いした。すると先方もやる気になってくれた。」
「やっぱり本気で想いを伝えなければいけませんね。うちらしい話です!」
「うん。その気持ちが本当に大事。加工後の精度を上げたいので金型の面粗度は極力小さくする必要がある。つるつるに仕上げてもらいたいことを伝えた。そのためには『とても潤滑性の高い油』が必要なのはわかっていた。過去に強絞り加工をしているメーカーがなんと天ぷら油を材料に塗布しているのを見たことがあったからね(笑)」
「天ぷら油ですか!」
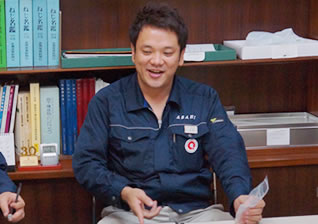
「見たときは本当にびっくりしたけど、あれは理に適っている。その経験をヒントに潤滑性の高い油を探し回った。そしてとうとう良い油を発見!その油は、水の中に漬けた負荷のかかったコロが回るくらい素晴らしい潤滑性を持っていた。金型メーカー様もびっくり!使ったことがない油だったからこそ使う前から興奮したね。実際に使ってみると期待通りの仕上がりだった。」
「嬉しいですね!」
「やっぱり期待通りの結果だと嬉しい。『このねじは作ることができる!』と確信した。そして次は材料の選定に移る。真っ先に頭をよぎったのはセオリー通りの材料ではうまくいかないだろう、ということ。つまり高炉から出てきた線材を普通のやり方で伸線したら絞った際に硬すぎて満足いく絞りができない。そこで神戸製作所様の特殊な材料を使ったナマシを用いることを思いついた。最初に減免率を上げて伸線を行い、炉にてナマシ加工を実施。その後もう一度伸線加工を実施。極めてやわらかい材料でないと実現できないので最後は肌抜けしないギリギリのところでスキンパス(伸線)をしてもらった。」
「材料にこだわる、という後藤部長がいつも仰っている意味がよくわかりました。」
「本当に材料は大切。準備が整って早速加工にトライ。結果は成功!30,000本すべてが焼付くことも、工具の破損もなく絞ることが出来た!見てもらうと『ダイスのジョイント部が剥離しています。でも30,000本も絞れたということはこの状態でなじんでいるとしか考えられませんね!』とのこと。珍しいケースだけど成功したのは事実。改良を加えて第2、第3の金型を製作してもらうことに。ここからは意外とスムーズ。金型の修正を数回経てヘッダーブランクが完成!あとは2種類の転造加工だけ。ローレットとねじのダイスを作り、ビスが完成した。」
「成功に至る背景やプロセスが目に浮かんできます。」
「もっとも問題だった工程を省くことができ、それにより納期短縮が可能になったことでお客さんも大喜び。もう一つの問題だった選定は自動選別機で行ったことで、加工漏れや不良品が流出しなくなった。そして単価も安くなった。何よりお客さんが本当に喜んでくれて良かった!」
「本当に良かったです!また色々と教えてください。貴重なお話ありがとうございました!」